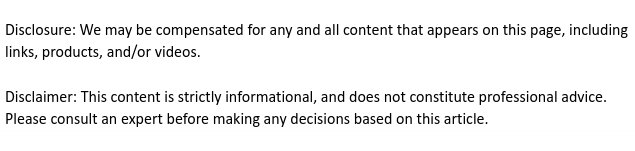
Trying to decide whether to rent or buy heavy machinery parts and equipment for your company requires a careful understanding of many factors. You don’t want to go into this process blind or start buying items because they seem cool. Here are the five most important factors that you need to consider to ensure that you find products that meet your needs as a company.
1. The Cost of the Equipment
If you’re ready to buy heavy machinery parts or full pieces of equipment, you need to make sure that you consider the cost. That’s because when you’re debating heavy equipment for sale for your team, you may be spending hundreds of thousands of dollars. It’s not uncommon to find some pieces of equipment that will set you back an excellent half a million, depending on what you are buying for your shop.
Therefore, it is crucial to consider various cost factors when looking at equipment to buy or even when deciding on forklifts for rent. Doing so will help you save money and ensure that you get the equipment that you deserve. So let’s take a look at some of the most common factors that affect the price of your equipment and what to consider when buying any of these items for your operation:
Renting vs. Buying — Some people may decide to rent pieces of equipment because the initial cost is lower. However, buying cuts back on long-term expenses and might be a good idea if you’re planning on expanding your heavy machinery options. Try to consider your bottom line at all times here.
Equipment Usage — The usage of your equipment will dictate your costs in many ways. For example, if your machinery is extensive and designed to handle many specialized tasks, you can anticipate that it will cost more than a small item that does only one or a handful of things well.
Branding — This might surprise you to know, but the branding of your equipment can heavily affect its price. More prominent manufacturers, like Caterpillar, ask for more money for their items by virtue of being who they are as a company, which will end up costing you more than if you buy from another source.
Ultimately, when you’re looking to buy heavy machinery parts or other items, you need to make sure that you balance your investment cost with the benefit that the machine provides for you. If you find that an item only provides minimal benefits or doesn’t quite fit into the operational guidelines of your shop, you may want to pass on it. However, if you feel like it is too beneficial to ignore, you should buy or rent it to help your operation.
2. Overall Equipment Safety
Here’s a fact that you need to understand when you try to buy heavy machinery parts or equipment: machinery accidents cause at least 35% of all on-the-job injuries and cause 14% of all deaths on work sites. Many of these problems are related to human error, but some may occur due to insufficient equipment safety steps or companies that don’t take this process seriously enough for their customers’ needs.
Therefore, you need to work directly with the manufacturer or dealer and ask them about safety concerns with your equipment. These questions are essential to consider because you don’t want injured workers triggering potential lawsuits or long-term compensation payments. Most importantly, you don’t want people who’ve worked with you for years to suffer because of your mistake. Questions to ask include:
- Does It Pass Safety Guidelines? — Ask the seller or manufacturer to show you proof that this piece of equipment passes essential safety guidelines, including showing any documentation from an inspector. If they refuse to show you such information, never buy a piece of machinery from them again.
- What Safety Extras Does It Include? — When you buy heavy machinery, you want to try to find items that have automatic safety features. For instance, you should find bulldozers that have an automatic turn-off when the driver leaves their seat. Doing so will avoid crushing deaths if they’re thrown off the rig.
- Are There Any Past Safety Concerns? — Research all pieces of equipment that you purchase for any potential safety problems that have been noted in the past. You should easily find examples of these issues if they have occurred, including machine failure, injuries, or deaths.
As a result, you need to consider this process when you buy heavy machinery parts and equipment. Even if you operate a business that sells diesel performance supplies, it is critical to spend time debating the safety of a piece of equipment. Many companies don’t take the time to consider this factor, even when discussing trailer rental for hauling their items. So make sure that you don’t fall into this negative behavior and take steps to ensure that you find the best equipment possible for your needs.
3. Equipment Operation
Do you know how to operate the heavy machinery that you’re considering buying? Or do you understand what it does and how it provides these services? If not, you shouldn’t try to buy heavy machinery parts or equipment outside your range of understanding. And yet, many people attempt to do that every year and cause a lot of concerns. This problem is something that can impact not only your operation of this equipment but also impact towing safety and other elements of safety.
Therefore, you need to take the time to acquaint yourself with the operation of each piece of machinery to ensure that you feel comfortable working with them. During this process, you’ll be gauging the ease of operating the equipment and whether you think it would work for your team. Remember: you likely have some experience with other pieces of equipment and need to find machinery that suits your needs and skills. Meet this goal by considering elements like:
- The Layout of the Controls in the Cab — Ask the manufacturer or dealer for a schematic of the control system used by this equipment. Take the time to examine how it is connected, where the items are located, and how they are used. Once you fully understand this aspect, you can compare its ease of use with other pieces of equipment to increase your comfort level with the operation.
- Purpose of the Machine — All heavy equipment has at least one or two operations that help make them beneficial for your operation. For example, bulldozers allow you to move dirt, break down weak structures, and even haul some items with a trailer. Try to gauge what usage you’d get out of an item before you end up buying or renting it for your firm’s needs as a company.
- Complications With the Equipment — During your test run of the equipment, it is crucial that you fully understand any possible complications that may result while you work it. For instance, you may run into difficulties with certain types of operations, like lifting the arm of a forklift. Try to gauge why these issues occurred and whether they were an error on your part or something wrong with the machine.
As you can see, it is crucial to take the time to acquaint yourself with equipment operation before you buy heavy machinery parts or any other items from a dealer. Sit down with them and talk about how each of these items works and see if they’ll let you take a test drive. Take the time to get used to the layout of the controls and have the potential operators of the equipment take the same steps to ensure you are protected. Take these steps even if you’re looking at simple used trailers for your operation.
4. Dealer or Manufacturer Reliability
Another element to consider before you buy heavy machinery parts is the reliability of the dealer or manufacturer with which you are working. You need to think of this process as if you were trying to find a used auto for sale for your company. It is critical to think of the dealer’s reputation and whether they are worth your time or if you should ignore them and work with another.
There are a few different ways that you can approach this process to ensure that it goes well for you. You’ll need to do a little research before you ever talk to the manufacturer but will also need to speak with them directly to learn more. This process will require you to have a little patience and understand the different steps necessary to ensure you find equipment that meets your needs. Just a few ways you can research dealer and manufacturer reliability include:
- Online Reviews — Take the time to read customer reviews for these businesses to get a feel for their capabilities and to understand whether they are right for you. Understand, though, that thoughts aren’t always 100% fair and may be biased based on minor problems or issues.
- Product Reviews — Many independent websites provide high-quality reviews that examine the pros and cons of heavy machinery. Understand, though, that some of these sites may be sponsored by these businesses and may tweak their approach to focus on that manufacturer or dealer.
- Better Business Bureau Reports — Search for your company online and see if they are registered with the Better Business Bureau. If not, that should raise a red flag with you. Find any reports related to this business, such as any problems that they have caused or safety issues with their equipment.
Make sure that you consider all of these aspects before you buy heavy machinery parts or equipment. It would be best if you also thought of some elements that may not have affected you otherwise. For example, suppose a piece of equipment requires regular temperature control to stay strong and safe. In that case, you’ll need to consider heating oil prices for any necessary heating equipment to provide your equipment with safe operation.
5. Environmental Safety
Heavy equipment typically utilizes a lot of heavy diesel fuel that can produce a lot of carbon emissions. As a result, you need to seriously consider the environmental safety of your items before you buy heavy machinery parts or equipment. A growing number of manufacturers find ways to make these items less damaging to the environment and more beneficial to their operators.
So whether you run a custom metal fabrication company or any other type of business, you need to take the time to examine the safety of each piece of equipment you buy. Most manufacturers are following the green trends to help save money and get rewarded for their efforts. Those who try to hide elements like the aspects below may be taking no or only minimal steps in this direction:
- Emissions Control — What steps does the manufacturer take to cut back on emissions? Have they created more efficient engines or better fuel filters to avoid long-term environmental damage? Contact the manufacturer directly to learn more about the steps that they’ve taken to meet this need.
- Fuel Usage — While most pieces of equipment are pretty efficient thanks to using diesel, make sure that you get a good understanding of their overall fuel efficiency. Try to buy machines that are more efficient or as efficient as possible to minimize the dangers of polluting the environment.
- Ease of Operation — Environmental safety is mainly tied to emissions and fuel usage and has other factors to consider. For example, more accessible equipment will be more efficient because your workers will spend less time struggling with the controls or figuring out how a machine works.
Consider these steps if you are operating just about any construction or manufacturing firm, such as a product design company or any important firm like it. Ensure that you try to find as many efficient items as possible and integrate them into your operation. Syncing them up with your overall manufacturing or production process will ensure that you cut back on operational costs and make it easier to buy heavy machinery parts and equipment later.
Taking Great Care When Purchasing Heavy Machinery
If you want to make sure that you buy heavy machinery parts and equipment that meets your needs, follow these simple steps. Don’t hesitate to reach out to other experts if you struggle to understand any of these steps or aren’t sure what to expect. These manufacturers will be more than willing to explain their equipment to you, especially if they believe it will lead to a sale on anything.